Digital twin technology has allowed for a greater understanding of and control over physical processes through the use of digital replication. This has opened the door for revolutionary advances in several industries.
Let's examine the various kinds of digital twin software that are revolutionizing the way companies innovate and run their operations.
1. Product/Asset Twins
Digital replicas of actual goods or assets that are intricate, dynamic virtual models are known as "product or asset twins." These digital twins are essential in areas like manufacturing, automotive, and energy, where the upkeep and performance of certain assets are crucial to overall operational effectiveness.
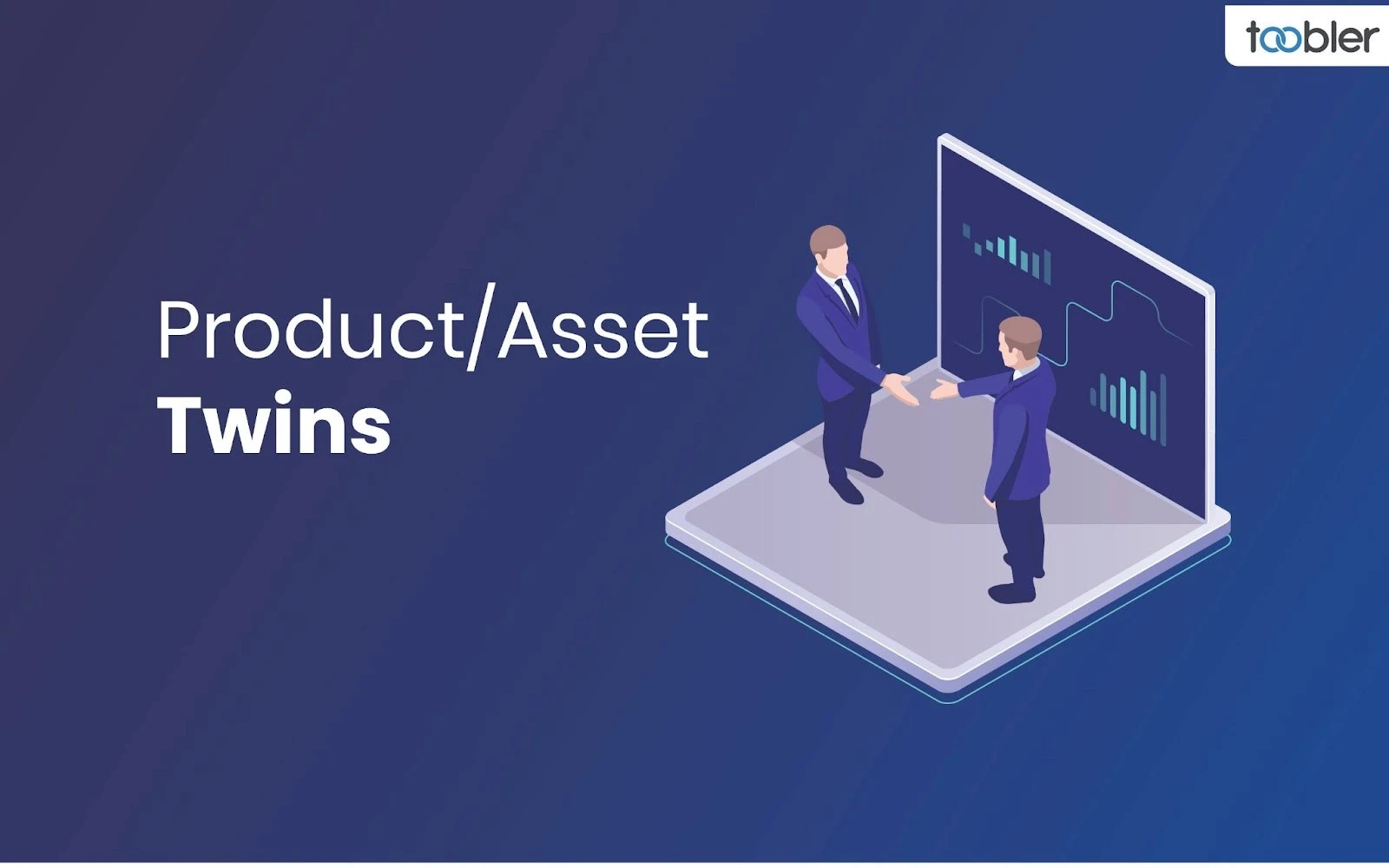
Key Applications of Asset/Product Twins
Digital twins may continuously monitor the operating state and overall health of vital assets. The integration of IoT sensors and analytics makes real-time tracking of several metrics, including vibration, temperature, pressure, and more, possible.
In order to make sure that heavy machinery, HVAC systems, and engines run within safe and effective operating norms, continuous monitoring is essential.
By using information from ongoing observation, digital twins can anticipate possible problems before they arise. Advanced algorithms that forecast wear and tear by analyzing trends and patterns make proactive maintenance solutions possible.
This method prolongs asset life and lowers operating costs by optimizing the maintenance schedule and preventing unplanned equipment failures.
Benefits of Product/Asset Twin Implementation
I. Increased Dependability and Customer Satisfaction
Businesses may significantly increase reliability by making sure items operate consistently at maximum efficiency. For instance, keeping equipment operating at peak performance is essential for customer confidence and safety in industries like aerospace and automotive. This is where equipment failure can have catastrophic consequences.
Digital twins make this possible, enabling businesses to monitor asset performance and conditions in real-time, improving overall trustworthiness and customer happiness.
II. Cost-effectiveness
Digital twins' predictive capabilities limit the need for periodic assessments and the likelihood of unforeseen malfunctions. These scenarios could result in costly repairs and lost production time.
Businesses may better distribute resources and schedule maintenance during off-peak times. Thereby, it prevents the high expenses of sudden breakdowns by precisely estimating their maintenance needs.
Application in the Automotive Industry
Digital twins in automotive areas, especially, automobile engines serve as an example of how this technology is transforming the automotive sector. Automakers utilize digital twins to build incredibly realistic engine models that gather information from several sensors. This configuration makes it possible to monitor engine health and performance in real-time.
Proactive maintenance can increase a vehicle's lifespan and dependability by warning engineers about possible problems like overheating or unusual wear and tear before they result in a breakdown. It not only keeps expensive issues on hold and improves car performance, but it also increases brand confidence among consumers.
Also Read: Top 10 Use Cases of Digital Twin in the Automotive Industry
2. Process Twins
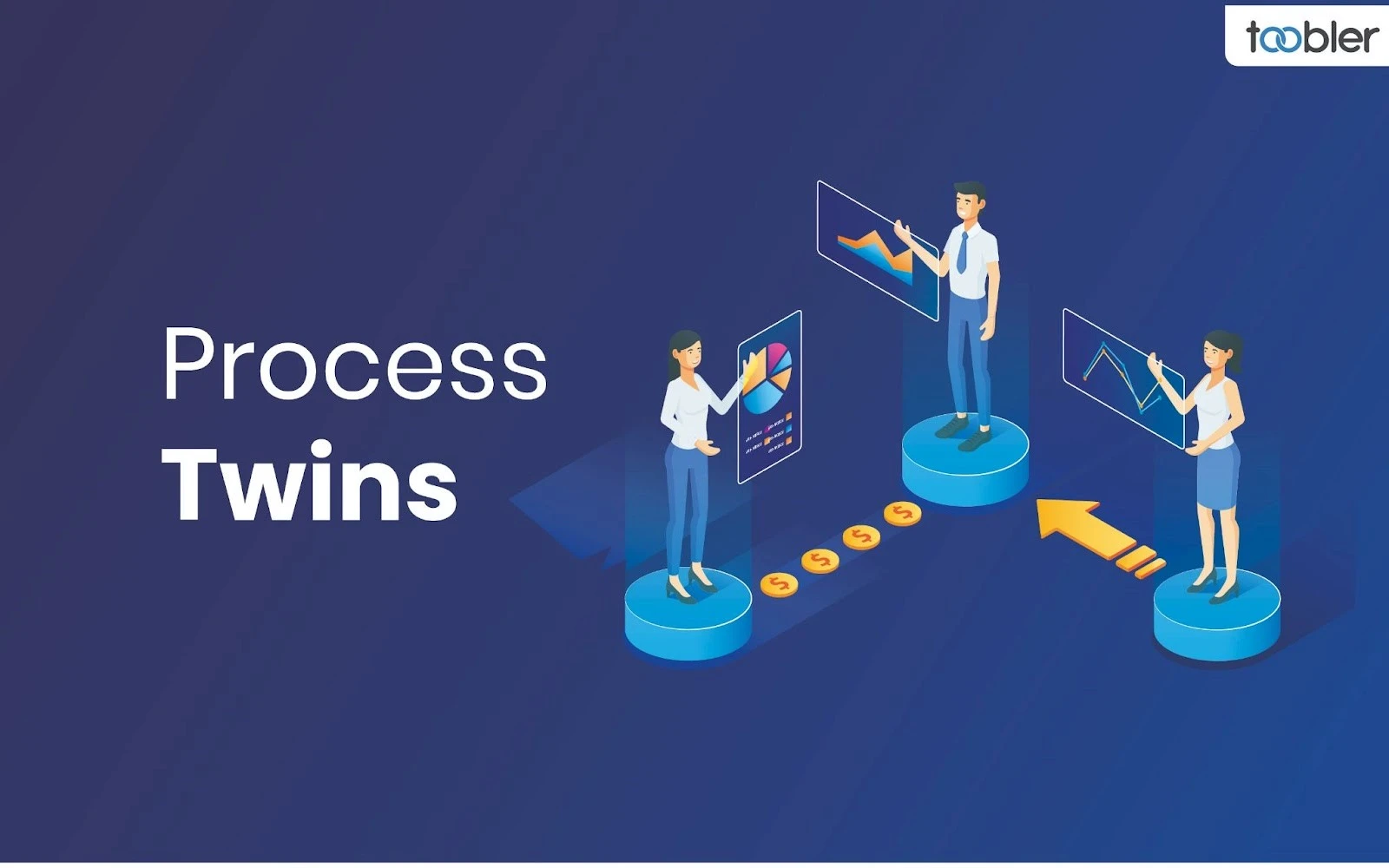
Process twins are an advanced type of digital twin technology intended to replicate and enhance corporate processes. This technology is very important in sectors like manufacturing, logistics, and utilities, where operational workflow reliability and effectiveness are critical. Process twins enable firms to assess and enhance their operations without interfering with real processes by generating a virtual clone of a workflow.
Key Applications of Process Twins
Process twins are used to visualize and pinpoint operational flaws and bottlenecks by modeling current procedures. With the help of this feature, companies may carefully review every stage of a process and apply changes in a safe, controlled virtual environment.
Businesses may improve procedures for effectiveness before implementing changes in everyday life by digitally testing the changes.
Training staff on complicated procedures usually takes a lot of time and risk, especially in sectors like aviation or chemical manufacturing. Process twins allow employees to train and acquire new skills in an accurate and realistic setting, free from the real-world penalties of making mistakes. This improves overall production security and efficiency by guaranteeing that employees are better equipped for their responsibilities and enhancing learning outcomes.
Benefits of Implementing Process Twins
I. Enhanced Operational Efficiency
Process twins assist businesses in improving efficiency and simplifying processes by enabling them to customize their procedures in a virtual environment. This improvement results in improved resource management, quicker turnaround times, and eventually increased overall effectiveness.
II. Decreased Training Costs
Traditional training methods can be pricey because they use expensive materials and equipment or require downtime. By moving a large portion of the training to a virtual environment, where the only expenses are for the system's initial setup and upkeep, process twins can drastically reduce these expenditures.
II. Enhanced Employee Competence
Through comprehensive simulations, workers acquire a more profound comprehension of their responsibilities and the systems they will handle. As a result of this readiness, staff confidence can rise, operational errors can be reduced, and employees can integrate into real work environments more quickly.
Application in the Manufacturing Industry
Process twins have revolutionized the management of production lines in the industrial industry. A business might, for instance, employ a process twin to model a new car assembly line to find any possible workflow inefficiencies.
By modifying the virtual model and tracking the results, engineers may design the most efficient assembly procedure.
Digital twin in manufacturing industry creates simulation that reduces the risk and expense of conducting physical testing and optimizes the manufacturing flow.
Line workers can be trained using the same process model after the ideal workflow has been determined. New hires can engage with the twin to learn about their duties within the assembly process. It ensures that they are adequately trained and acquainted with their responsibilities before they ever set foot on the plant floor.
This strategy improves the facility's overall efficiency as soon as it goes live and eases the switch for fresh hires.
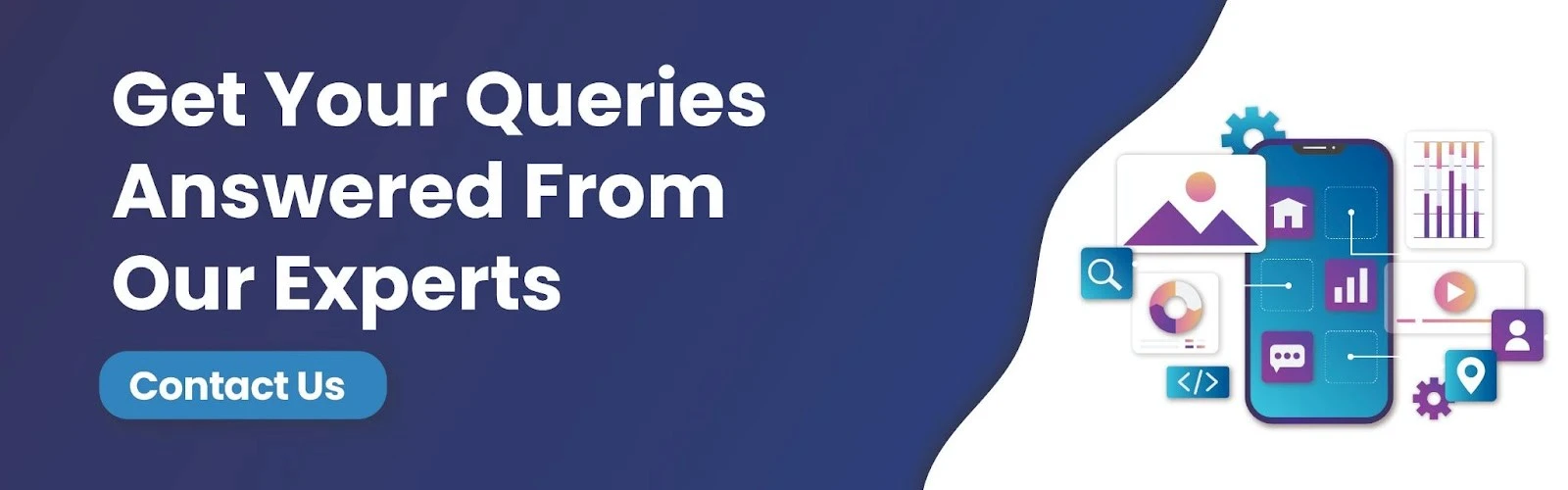
Also read: 10 Steps for Successful Digital Twin Implementation
3. System Twins
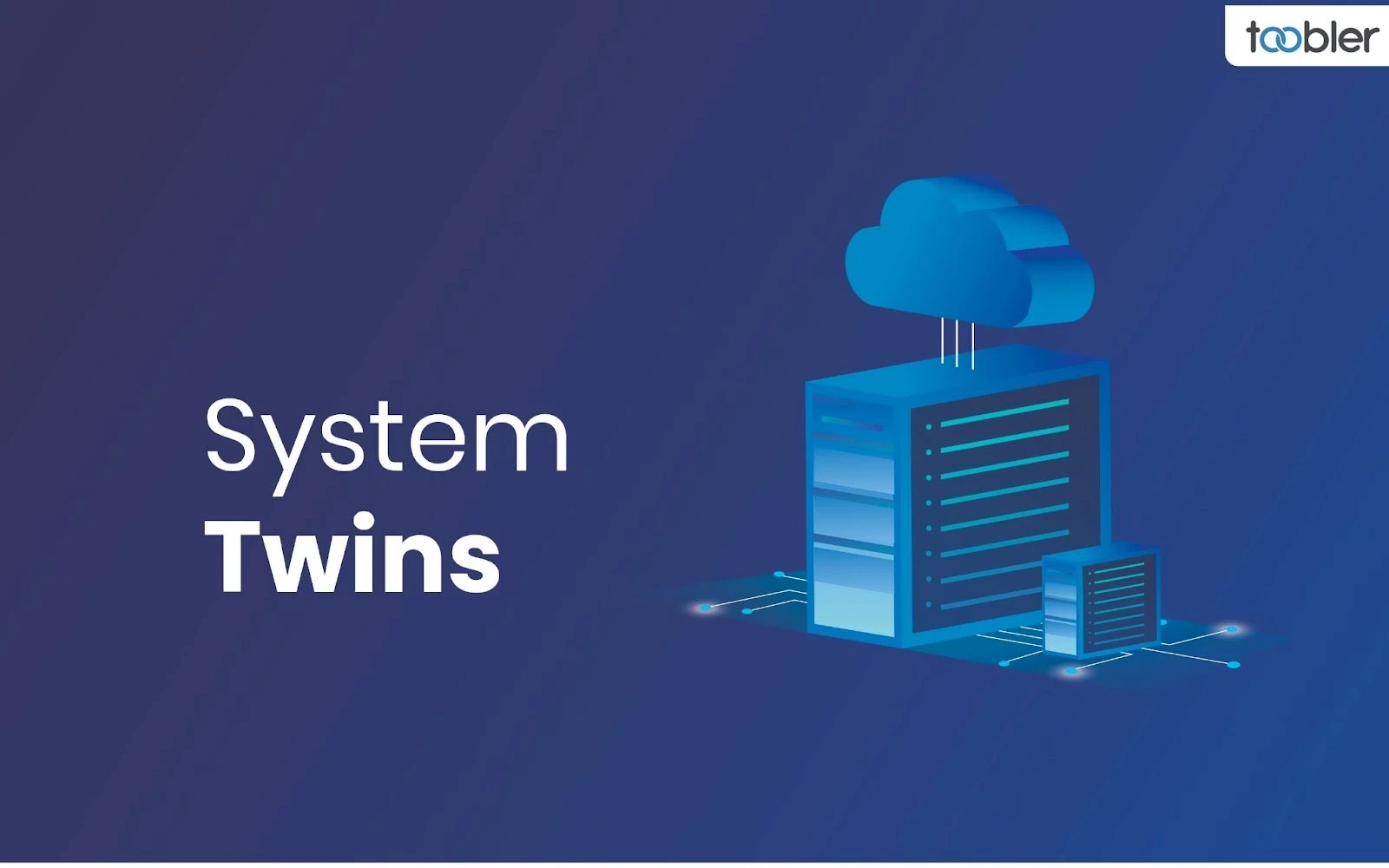
A complex subset of digital twin technology called system twins is made to combine different parts or procedures into a single, all-inclusive system model. They give an overview of the entire operation at a large scale and reveal insights that are not apparent at the micro level.
This comprehensive method works exceptionally well in settings where several subsystems depend on one another, such as massive construction projects, smart cities, and production plants.
Key Applications of System Twins
System twins are essential for system integration testing because they mimic how various system components communicate with one another. This testing aids in the identification of compatibility problems and possible points of failure among networked systems prior to deployment in real-world circumstances.
Through integration testing with system twins, companies can make sure that every component of the system works together and communicates as intended, preventing expensive and disruptive problems after deployment.
System twins are very useful for managing complicated systems since they can give an overview of every facet of the system's operations. They make it possible for leaders and managers to maintain and improve the functionality of the system as a whole, not just its parts. Ensuring system efficiency requires this vigilance, particularly in situations where the functioning of one component might have a significant influence on others.
Benefits of System Twin Implementation
I. Improved Insight and Management
From manufacturing processes in factories to traffic flow in cities, system twins provide unparalleled insight into the inner workings of complex systems. Managers may make well-informed decisions that maximize performance and avoid bottlenecks due to this insight.
II. Proactive Problem Solving
One of system twins' greatest benefits is their capacity to anticipate and resolve systemic problems before they worsen. System twins are useful tools for preventing issues that could cause malfunctions and downtime because they can forecast how changes to one component of the system might influence others.
Application in Smart City Industry
The use of system twins in smart city initiatives is a prime example. System twins are utilized in these projects to oversee and combine services, emergency services, traffic systems, and public transit.
City administrators and planners can employ system twins to ensure that all of these elements function as a whole, which will improve citizen quality of life and increase operational efficiency.
Also Read: The Role of Digital Twin Technology in Smart Cities Development Here.
4. Component Twins
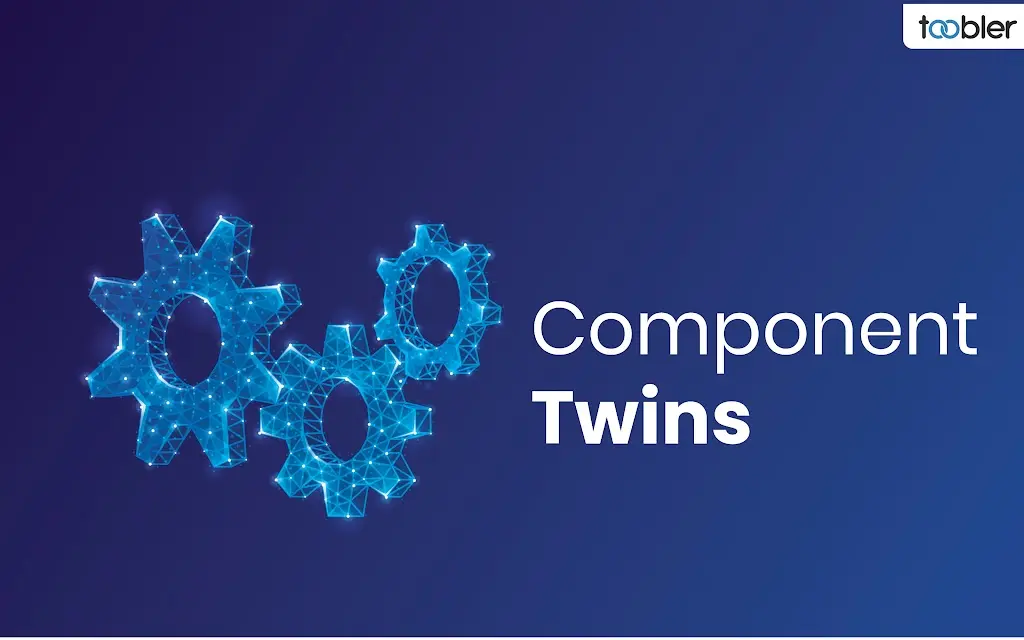
Component twins represent the most complex kind of digital twin technology, concentrating on specific parts of a system or product. These digital copies are essential in domains where accuracy and dependability are crucial because they offer a microscopic picture of a component's lifespan, from design to operation.
Key Applications of Component Twins
Component twins provide in-depth information about the functionality, state of health, and performance of certain components. These digital twins constantly gather data from sensors integrated into the component.
This allows them to track variables like stress, pressure, and temperature in real-time. Predicting maintenance needs and maximizing component performance require this level of data.
By using component twins throughout the design phase, engineers can simulate and assess how a part will react under different operating situations. This utilization is essential in sectors where efficiency and safety are vital, such as the aerospace and automobile industries. Engineers can also quickly iterate ideas without incurring the costs associated with actual prototypes by virtually testing components.
Further read: Overcoming Digital Twin Implementation Hurdles | Toobler
Benefits of Component Twins Implementation
I. Improved Tracking and Service
Digital twins enable focused maintenance operations that can prevent more significant system failures by enabling accurate component-level monitoring. This proactive maintenance strategy extends the component's life and improves the system's overall reliability.
II. Time and Money Savings in Design and Testing
Component twins reduce the time and money needed for the design and testing stages. These digital twins help firms avoid expensive redesigns and expedite the approval of new ideas by spotting possible design defects early in the development process.
Application in Aerospace Industry
Component twins are widely employed in the aerospace industry to represent crucial components of an aircraft engine. Engineers use these computerized models to forecast how each part will function in different flying scenarios, such as variations in temperature or altitude.
Aerospace businesses can reduce the risks associated with innovative designs and make sure every item satisfies stringent safety regulations by using component twins to undertake extensive testing prior to manufacturing.
Moreover, continuous monitoring made possible by component twins aids in anticipating failures of parts, improving maintenance plans, and eventually resulting in a secure and dependable aircraft.
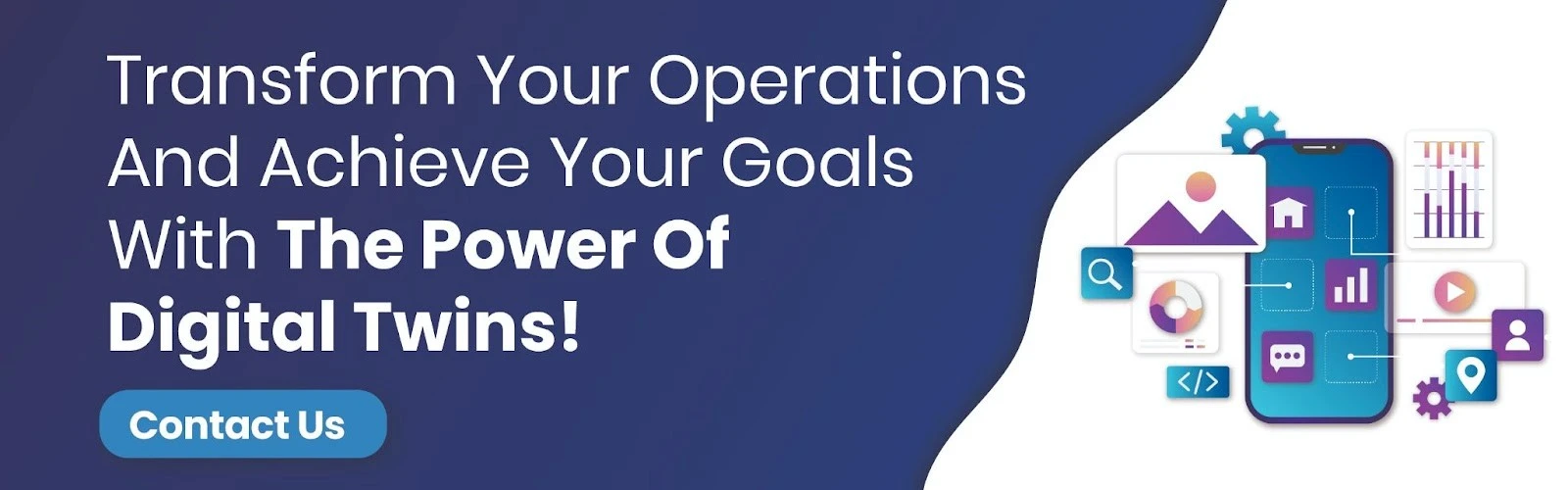
Please read: Sustainability with Digital Twin for Environmental Conservation | Toobler