Designing digital twin solutions for manufacturing requires a methodical, systematic approach. Every stage guarantees that your solution uses the newest technologies to produce quantifiable outcomes and is in line with your operational objectives. Let's break it down into manageable steps.
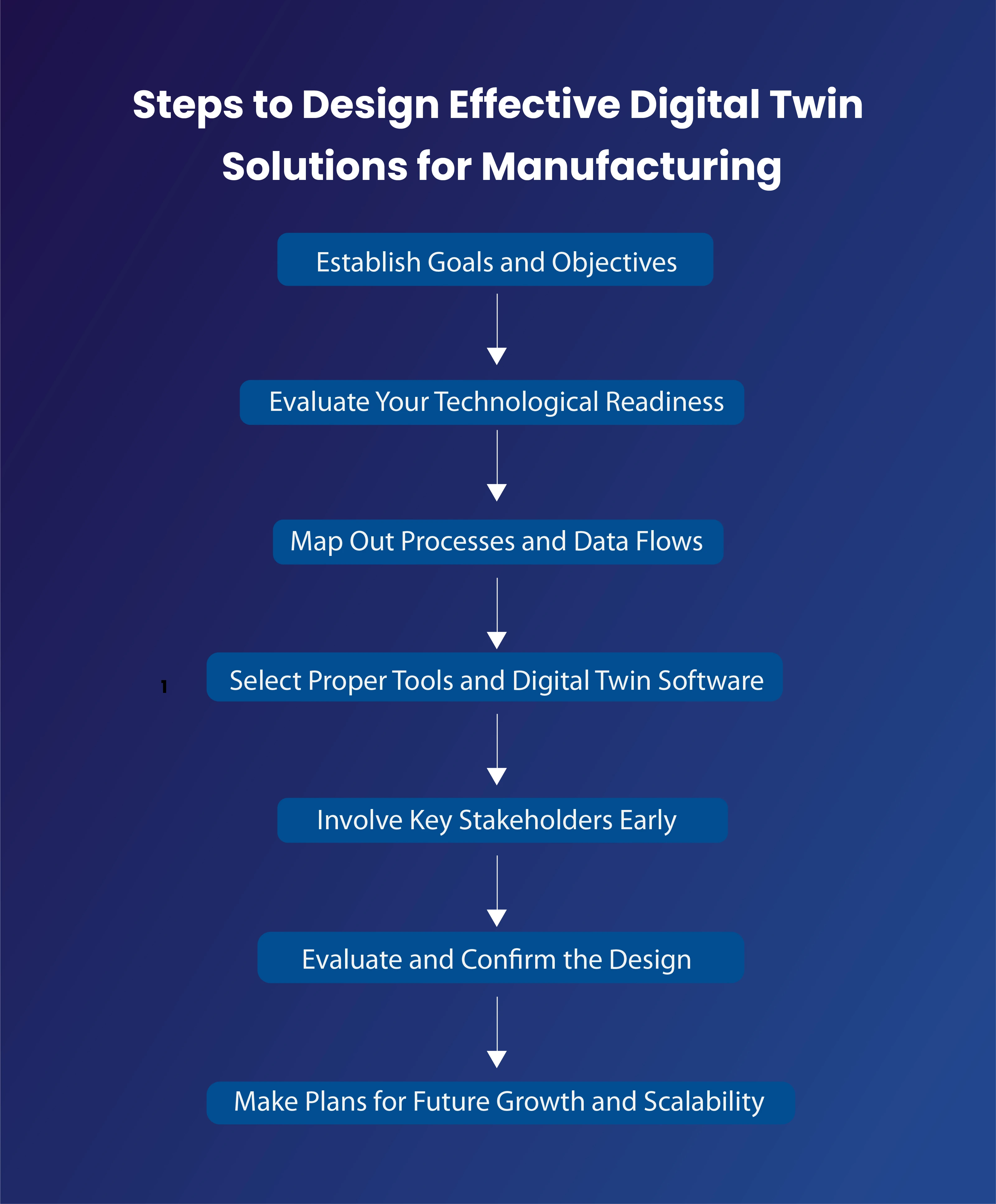
Step 1: Establish Goals and Objectives
Have you ever started a project without understanding what defines success? Even the best technologies can fail if the goals are unclear.
Why Begin Here?
Setting clear objectives guarantees that your digital twin will provide genuine value. Respond to these questions first.
Is reducing machine downtime your goal?
Are you aiming to improve the quality of the product?
Are you looking to increase the effectiveness of production?
Pro tip: Make sure your objectives are SMART—Specific, Measurable, Achievable, Relevant, and Time-bound.
Step 2: Evaluate Your Technological Readiness
If your existing systems cannot accommodate a digital twin, what good is it? It's similar to ensuring your automobile is fueled before a road trip to evaluate your tech stack.
Essential Things to Consider:
IoT Connectivity: Do your machines have IoT sensors installed?
Data Infrastructure: Is your data accessible, well-structured, and clean?
Software Compatibility: Are digital twin apps compatible with your present systems?
Remarkably, just 55% of manufacturers worldwide have digital twin integration-ready IoT-enabled systems.
Please read: Digital Twins and IoT
Step 3: Map Out Processes and Data Flows
Consider duplicating your processes without being aware of the precise procedures required. Process mapping guarantees that your digital twin faithfully captures reality.
Methods for Process Mapping:
Record each process step, from acquiring raw materials to delivering the finished product.
Determine the crucial moments when gathering data is necessary.
Draw attention to any inefficiencies or bottlenecks that the digital twin can resolve.
Step 4: Select the Proper Tools and Digital Twin Software
What software will your digital twin be powered by? Choosing the appropriate instruments is essential for smooth functioning.
Important Points to Remember:
Is the program able to accommodate future growth?
Does real-time analytics offer insights that can be put to use right away?
Will it be compatible with your current ERP or MES systems?
Step 5: Involve Key Stakeholders Early
What happens if engineers or operators are not present? Resistance to change can undermine even the most sophisticated solutions. Get your team involved right now.
Ways to Engage Them:
Organize workshops to discuss the advantages of digital twins.
Respond to their worries over job roles or changes to the workflow.
Include their suggestions in the design process.
Step 6: Evaluate and Confirm the Design
Test your digital twin in a restricted setting before a large-scale launch.
Testing assists in finding holes or malfunctions before they affect operations.
Step 7: Make Plans for Future Growth and Scalability
The manufacturing sector is changing quickly. A digital twin solution should adjust to the difficulties of the future in addition to meeting the demands of the present.
Questions to Ask:
Further read: Digital Twin in AI
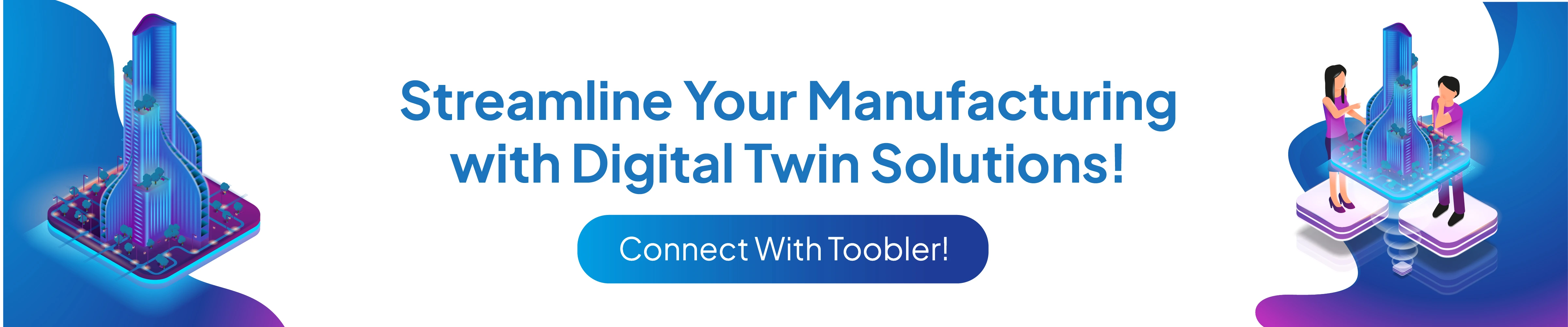