The oil and gas sector is no stranger to technological advances. And as we journey further into the digital age, the integration of digital twins is set to evolve and expand. Let's delve into what the future might hold for digital twins in the oil and gas sector:
Beyond just planning, digital twins might soon adjust drilling operations in real time based on immediate feedback from subsurface conditions. This helps in reducing the risks of non-productive time.
In places that are hard to reach or dangerous, we might see fully automated operations run by digital twins. This way, the human intervention is minimal and mainly supervisory.
Digital twins could simulate and predict customer behaviors at fuel stations. This could optimize services and tailor offerings, leading to a personalized customer experience.
Learn more about the relationship between digital twins and customer experience.
As the energy landscape shifts towards renewable sources, digital twins will play a pivotal role in integrating oil and gas operations with renewable energy sources, ensuring seamless energy transition.
Please read: Digital twin for sustainable business
Digital twin technology in the oil and gas industry guarantees smooth regulatory compliance by simplifying data collection and processing. Real-time process monitoring by operators guarantees compliance with safety and environmental regulations.
A digital twin pipeline, for instance, can monitor pollutants, allowing for proactive modifications to satisfy sustainability objectives. Utilizing digital twin oil and gas solutions promotes reporting transparency and lowers the possibility of non-compliance fines. It also emphasizes how crucial technology is to the oil and gas sector's ability to operate sustainably.
Establishing centralized platforms for cross-functional cooperation is one use case for digital twins in the oil and gas sector. Teams from different locations can effectively make well-informed decisions, model scenarios, and access real-time data.
Examples of digital twins in the oil and gas sector demonstrate how IT solutions improve communication during intricate projects like offshore drilling. By encouraging innovation and efficiency in operation, this enhanced coordination emphasizes the value of technology in the oil and gas sector.
Using digital twin technology to model changes in infrastructure or operations in the oil and gas industry lowers expenses and risks. Before implementing changes, operators can test them in a virtual setting to ensure ideal results.
A digital twin pipeline simulation, for instance, can forecast performance in various scenarios, preventing expensive downtime.
These digital twin use cases in the oil and gas industry highlight how crucial technology is to cutting costs and guaranteeing operational effectiveness in the fiercely competitive energy market.
Integration with Other Technologies
By embedding sensors in every conceivable piece of equipment, real-time data can be streamed continuously to the digital twin. This 'always-on' data flow can aid in achieving hyper-accurate simulations and predictions.
Learn how IoT helps Digital twins perform well
AI can enhance the predictive power of digital twins. For instance, while a digital twin can model a pipeline's behavior, AI can predict when and where the pipeline might fail based on vast amounts of historical and real-time data.
Ensuring data security and transparency is crucial. Blockchain can be used to validate and secure data transactions between the digital twin and other systems, guaranteeing the authenticity and integrity of the data.
Maintenance crews could use AR goggles to 'see' the digital twin's data overlaid on a physical asset, helping them identify problems faster. VR can immerse trainees in simulated emergency scenarios derived from digital twin models, offering hands-on experience without real-world risks.
For operations in remote areas with limited connectivity, edge computing can process digital twin data on-site, ensuring decisions are made quickly without waiting for data to travel to a central server and back.
As the oil and gas sector continues to face challenges, embracing the advanced capabilities of digital twins will be key to navigating the future.
Also read: 7 Best Digital Twin Companies To Look For In 2024
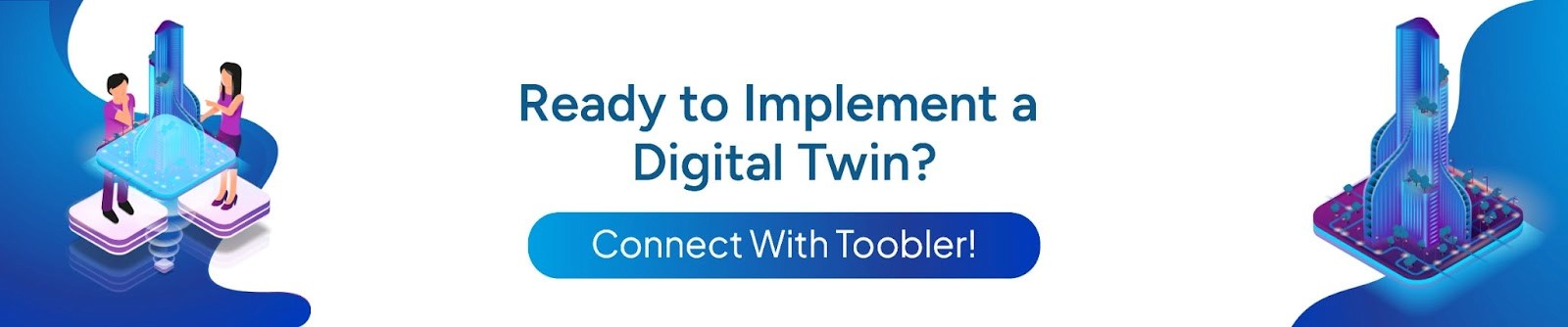