Digital Twins and the Internet of Things (IoT) represent a powerful synergy. Their interplay is a cornerstone of Industry 4.0, fostering innovation in various fields.
Consider digital twins in manufacturing, where every piece of equipment has Internet of Things sensors installed. These sensors gather information on vibration, temperature, and other essential factors.
The Digital twin receives this data continually and uses real-time processing and analysis. If the digital twin identifies a pattern that points to an imminent machine failure, the maintenance staff can avoid unscheduled downtime by taking proactive action.
Additionally, the Digital twin transforms manufacturing procedures by simulating different scenarios. For example, by altering particular parameters, the plant can maximize output while decreasing energy usage. On the other hand, using conventional techniques is almost impossible to reach this level of optimization.
Let's discuss it further.
How are Digital Twins leveraging IoT?
1. Data Collection
Digital Twins require a constant stream of data to effectively mirror their physical counterparts. And IoT devices embedded with sensors can help with this. These sensors collect data in real-time from the environment, user interactions, or the object's performance.
There are a lot of IoT devices available, each helping with interconnectivity and data collection. Therefore, digital twins can be fed with a variety of data points. This enriches the virtual representation and helps mimic its physical counterpart.
2. Real-time Monitoring & Analysis
As IoT devices transmit data, Digital Twins update in real-time. This ensures that the virtual model is always in sync with the physical entity.
Using the data from IoT devices, Digital Twins can simulate various scenarios. For instance, a Digital Twin of an EV, receiving data from IoT sensors, can simulate performance under different traffic conditions.
3. Feedback Loop and Continuous Iteration:
Post-simulation, Digital Twins can suggest optimizations. For instance, if an IoT-enabled HVAC system's Digital Twin simulates energy inefficiencies during peak hours. As a result, it might suggest operational changes to reduce consumption.
By monitoring wear and tear via IoT data, Digital Twins can predict when a part might fail. This leads to proactive or predictive maintenance, avoiding costly downtimes.
For systems that can be remotely controlled, Digital Twins can send adjustments back to the physical system in real-time based on ongoing analysis.
4. Virtual Prototyping & Testing
Before deploying a new system or making changes to an existing one, its Digital Twin can be used for virtual testing. IoT data from similar systems can be used to run these tests, reducing risks and ensuring smooth deployments.
Digital twins of complex machines or an entire workplace can be created to train and empower workers. This could avoid casualties and risk damaging expensive machinery.
5. Enhanced User Experience & Personalization
In consumer-centric sectors, IoT devices can capture user behaviors and preferences. The Digital Twin, using this data, can then aid in refining product designs or services.
For smart homes, Digital Twins can simulate user experiences based on individual preferences. This can help ensure a tailor-made interaction for every user.
6. Integration with Other Systems
Digital Twins aren't isolated. They often interact with twins of other systems. IoT provides the data layer that ensures these interactions are based on current and accurate information.
For instance, consider a smart city model. The Digital Twin of a traffic system might interact with that of a public transport system, using real-time IoT data from both.
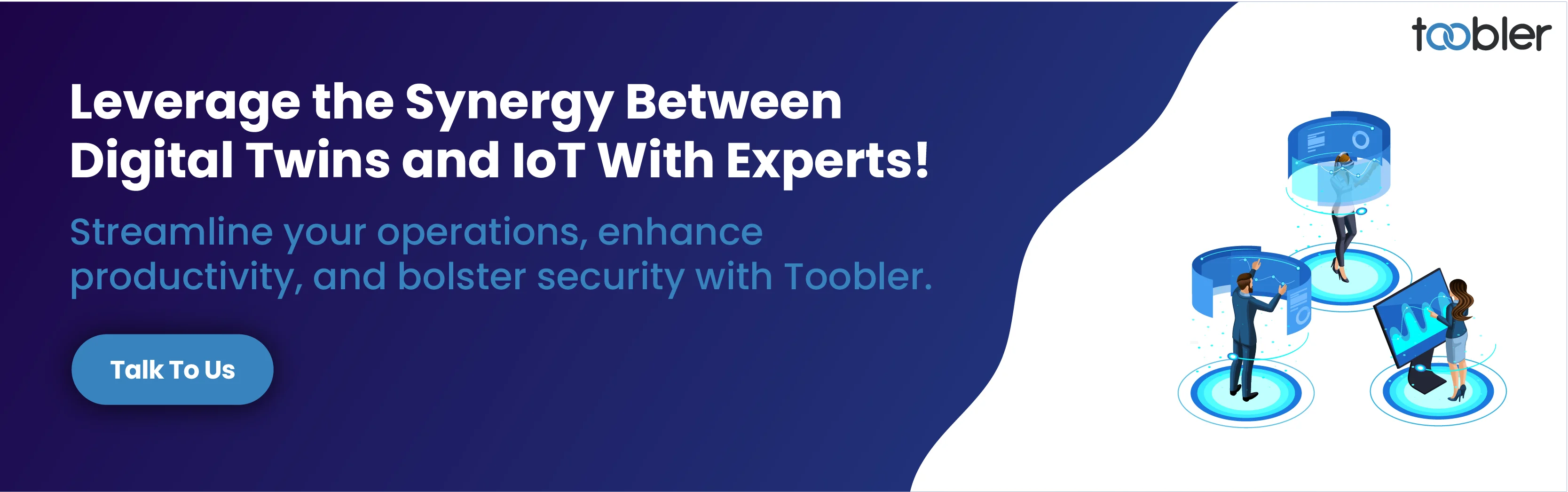
Also Read: How digital twins influence the automotive industries?